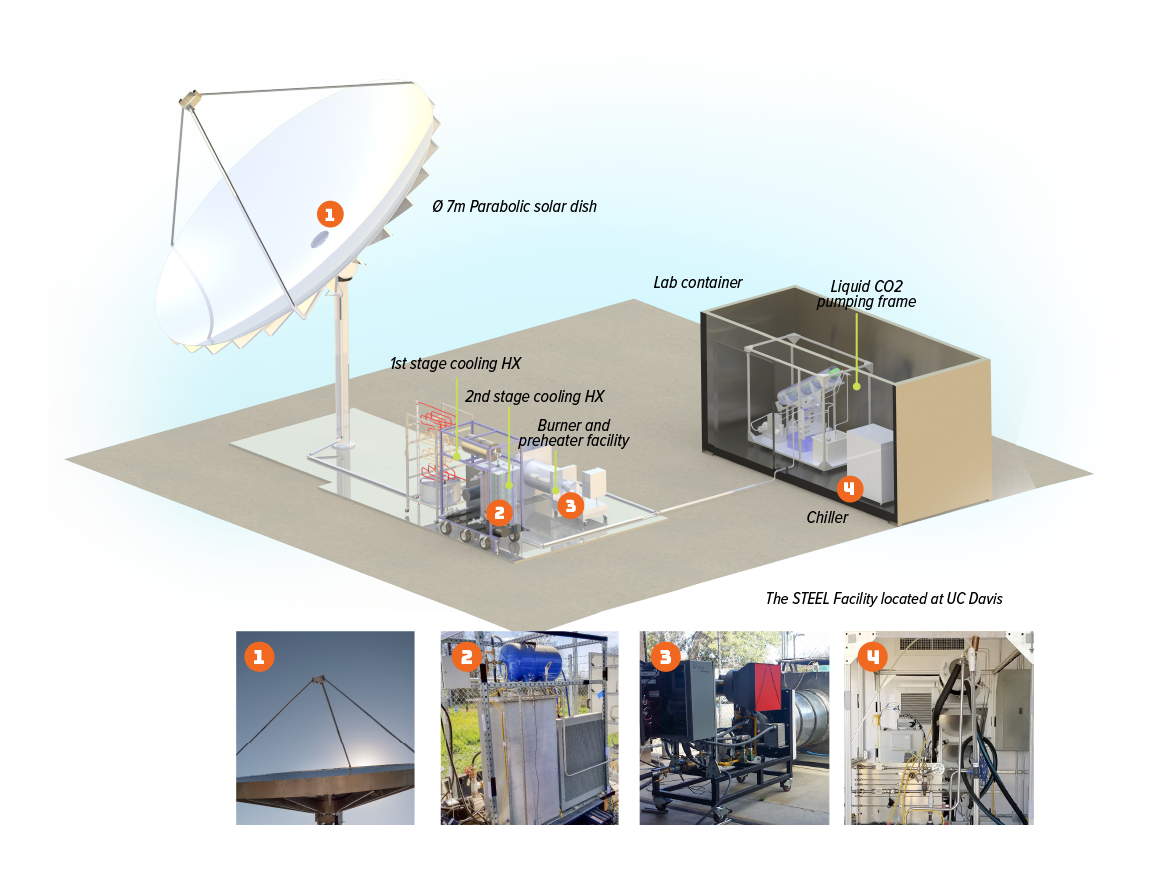
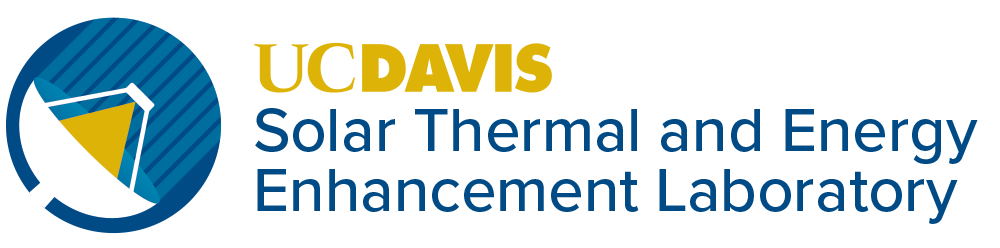
The Solar Thermal and Energy Enhancement Laboratory (STEEL) was developed to further research in advanced heat exchangers for a variety of applications such as solar power generation, thermal desalination, waste heat utilization, and solar fuels.
The STEEL facility is equipped with a 7-m parabolic solar dish that is capable of concentrating sunlight by nearly 1000 times at the focal area. The facility is also home to a high pressure (200 bar), high temperature (up to 700 C) supercritical carbon dioxide (sCO2) flow loop. The combination of the parabolic dish and the sCO2 loop give the UC Davis STEEL lab a unique set of capabilities in the area of high temperature and high pressure heat transfer research, along with heat exchanger technology development.
Facility Capabilities
- System pressure: up to 200 bar
- sCO2 working temperature: in excess of 700°C
- sCO2 typical flow rates: 0.1 kg/s at differential head of 10 bar
- Heat source: Parabolic Solar Dish AND/OR Natural Gas burner
- Heat exchangers: Air cooled (39 kW cooling) and Shell and tube (38 kW cooling)
- Cooling source: 5-Ton (17.5 kW) air cooled chiller with coolant supply at minimum temperature of 3°C
- Flow rate measurement: Coriolis mass flow meter with accuracy of 0.1% of reading (up to 30 g/s at pressures up to 150 bar) and Turbine flow meter with accuracy of 0.5% reading (0.35 to 3.5 GPM at pressures up to 200 bar)
- Remote experiment monitoring and controlling enabled
- Cyclic and static pressure test range: 1-200 bar
- Test section temperature: Max up to 800 °C
- Test chamber size: 36” x 36” x 24” (height x width x depth)
- Equipped with a 500,000 BTU/hr (165 kW) burner
- Temperature and pressure calibrator: NIST traceable lab calibrator with 0.0025% calibration accuracy.
- Temperature calibration: NIST traceable RTD with calibrated accuracy of ± 0.006°C at 0°C for calibration of variety of temperature sensors.
- Pressure calibration: NIST traceable pressure modules for calibrating absolute/differential pressure transducers in range of 0-1 bar (±0.0175% FS), 0-7 bar (±0.025% FS), and 0-340 bar (±0.1% FS).
- Olympus BX60 optical microscope (4x objective) equipped with Amscope microscope digital camera, Edmund Optics 1951 USAF Hi-resolution target (58-198) and 0.125mm spacing Glass Distortion target (58-509).
- Access to other imaging methods such as Zeiss Confocal Axio CSM 700 optical microscope and neutron imaging through UC Davis shared services.
- 7-m diameter solar dish concentrator equipped with two-axis tracking.
- Ethernet and remote control enabled.
- Capable of supplying 900-1000 sun energy and 25 kW heat at the focal point.
- Maximum test section size: 30cm x 30cm.
- Equipped with fluidic lines to provide heat transfer fluid with up to 200 bar pressure and 550 °C temperature to the test section at the focal point.
- Equipped with a commercial solar thermal receiver capable of absorbing 25 kW concentrated solar heat.
- Can supply solar heated water at 60°C and 6 GPM.
- Equipped with a water pump capable of supplying 340 liters/min (89.8 GPM) at maximum operating pressure of 10 bar (145 PSI).
- Equipped with an air-cooled radiator with heat rejection of 36.5 kW at flow rate of 219.5 liters/min (58 GPM).
- Flow rate measurement: Turbine flow meter with accuracy of 0.5% reading
- High Speed Imaging System, Photron AX100 camera, capable of recording 4000 frame per second of images with 1 mega Pixel resolution. Array of lenses including large-focal distance microscope objectives, halogen light sources, and a workstation with gigabit Ethernet connection for fast download times from the camera.
- Dell Precision Tower T7910. 128 Gb DDR4 RAM. Intel® Xeon® Processor E5-2687W v4 (12C HT, 30MB Cache, 3.5GHz Turbo).
- Two Dell Precision Tower T7920. 64 Gb DDR4 RAM. Intel® Xeon® Gold 6130 (16C, 22MB Cache, 2.1GHz).
- Shared license to ANSYS Fluent, Matlab, Solidworks, LabView, and and EES (F-Chart) software.
Ongoing Projects at the STEEL Site
Microchannel Solar Receiver Development
Oregon State University (OSU) and UC Davis WCEC researchers are collaborating on developing a solar thermal receiver based on flow of sCO2 through microchannel pin fin arrays. The microchannel receivers designed by OSU are being tested at working pressure and temperature by WCEC and finally will be characterized by on-sun testing. For more information, visit:


Additively Manufactured High T&P Microchannel Heat Exchangers
Through a collaboration between UC Davis WCEC and Carnegie Mellon University, researchers are designing and fabricating novel additively manufactured heat exchangers to withstand internal pressure and temperatures as high as 200 bar and 800 °C with wide range of applications in waste heat recovery, concentrated solar power plants and other industrial energy production. To learn more visit:
DOE Project Profile: University of California, Davis
UC Davis Selected to Receive $2.2 Million Award to Advance Solar Technologies
CONTACT THE LAB MANAGER
Erfan Rasouli
erasouli@ucdavis.edu